How Does Industrial DataOps Enhance Predictive Maintenance?
Discover how Industrial DataOps transforms predictive maintenance, reduces downtime, and boosts efficiency with AI-driven insights and real-time data analytics.
share this
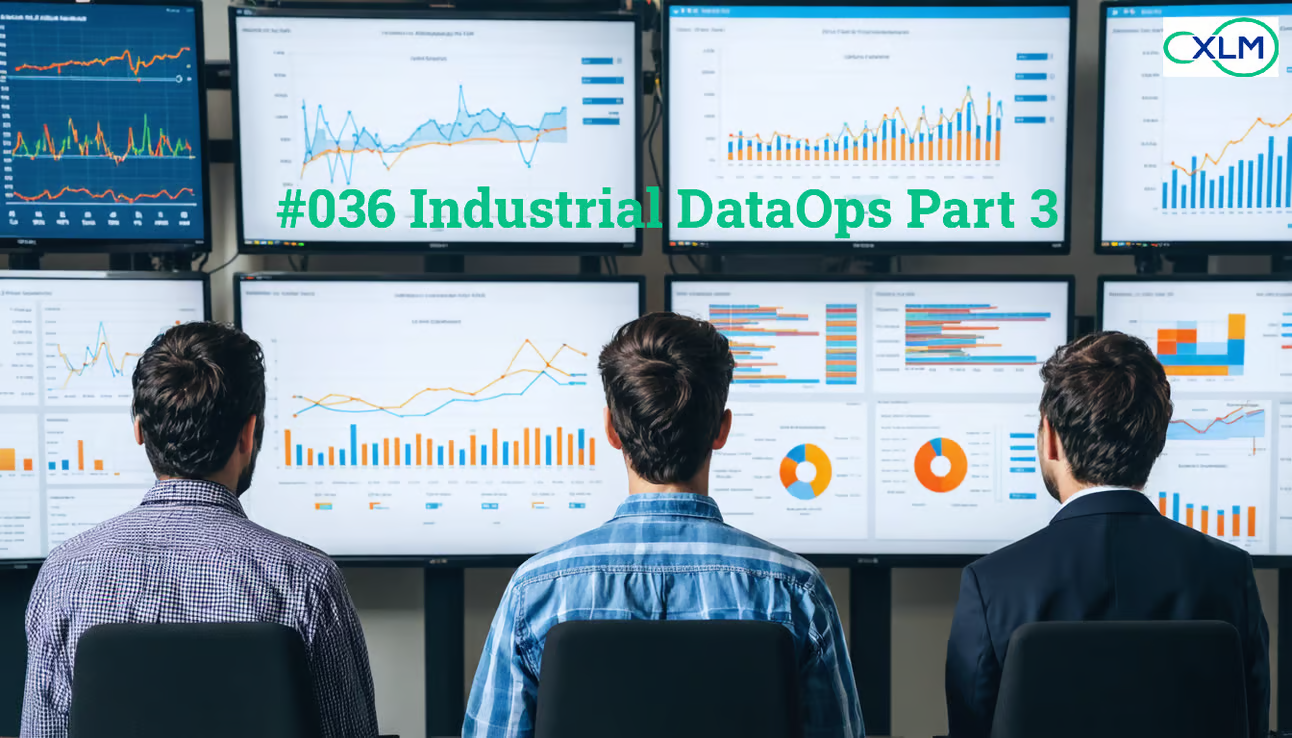
1.0. Introduction
The integration of Industrial DataOps with Continuous Predictive Maintenance (cPdM) is revolutionizing industrial maintenance strategies. By adopting data-driven methodologies, organizations can significantly enhance predictive accuracy, minimize downtime, and optimize operational efficiency. This guide covers the step-by-step process of implementing DataOps in cPdM, including:
- Data Gathering and Preprocessing
- Feature Engineering and Machine Learning Modeling
- Visualization and Reporting
2.0. Implementing Industrial DataOps in cPdM
Implementing Industrial DataOps in cPdM empowers organizations to effectively harness the potential of data analytics. Integrating Industrial DataOps into Continuous Predictive Maintenance (cPdM) empowers organizations to unlock the full potential of data analytics for smarter, more efficient maintenance strategies. By focusing on:
- Robust data gathering,
- Preprocessing techniques,
- Advanced feature engineering,
- Strategic machine learning modeling, and
- Insightful visualization dashboards,
companies can significantly enhance their predictive maintenance capabilities.
This proactive, data-driven approach reduces unplanned downtime, optimizes resource allocation, and boosts overall operational efficiency, helping organizations maintain reliable, cost-effective industrial operations.
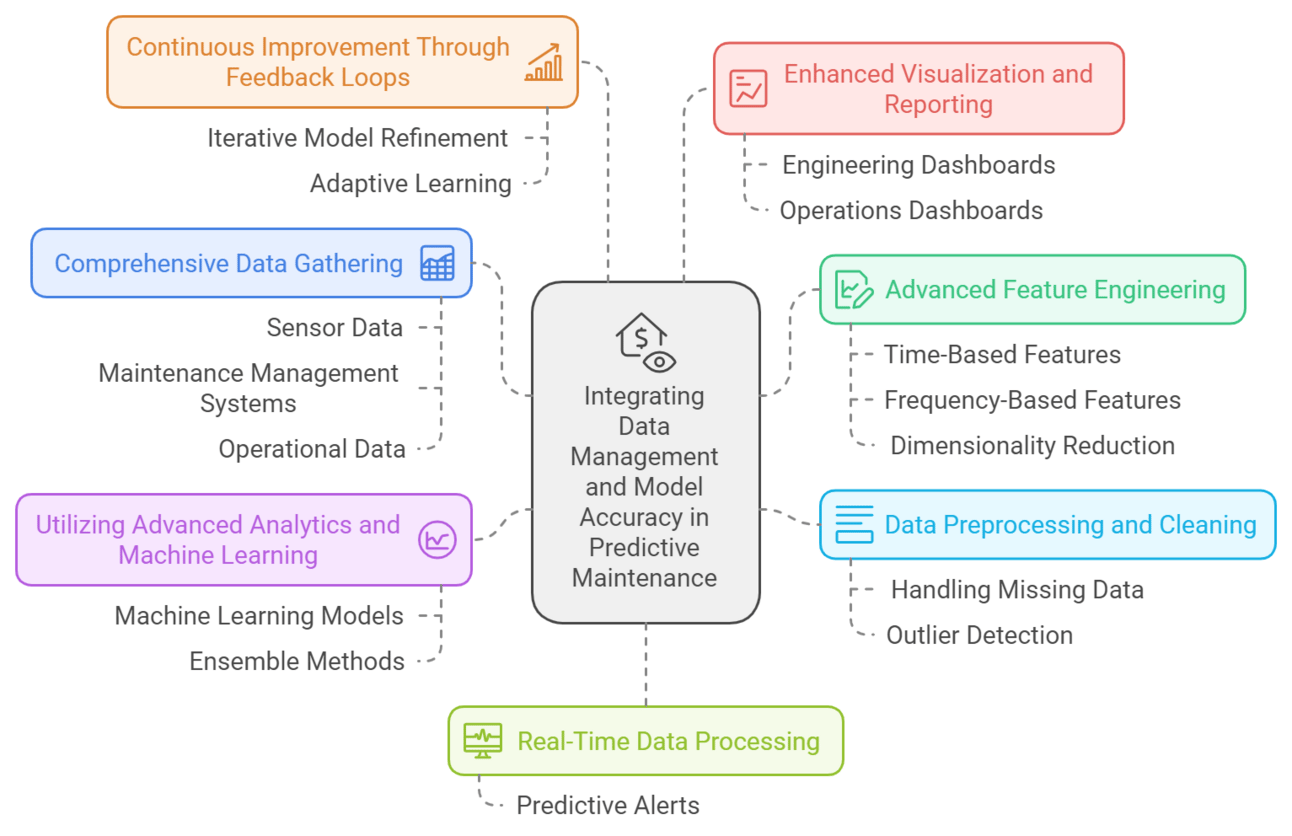
2.1. Data Gathering
Effective predictive maintenance relies on comprehensive data collection from various sources. Key data types include:
- Sensor Data: Sensors measure critical parameters such as vibration, temperature, and sound. For instance:
- Vibration Sensors: Detect early signs of wear and tear in rotating machinery using piezo accelerometers.
- Temperature Sensors: Monitor operational temperatures with RTDs (Resistance Temperature Detectors) and thermocouples to prevent overheating.
- Sound Sensors: Use ultrasonic microphones to capture high-frequency sound patterns and detect anomalies.
- Maintenance Management Systems (CMMS):
- Analyze historical maintenance records to identify patterns of past failures and repair logs.
- Supports failure pattern recognition and Remaining Useful Life (RUL) estimation.
- Operational Data:
- Data from industrial processes (e.g., production cycles, machine output) helps correlate maintenance needs with production demands.
2.2. Data Preprocessing
Data preprocessing is a crucial step in preparing high-quality datasets for machine learning models used in predictive maintenance (cPdM). Clean, standardized data significantly improves model accuracy and enhances failure prediction capabilities.
- Handling Missing Data:
- Deletion Techniques: Removing incomplete rows simplifies the dataset but may reduce sample reliability.
- Imputation Techniques: Use mean/median imputation or advanced methods like Multiple Imputation to fill missing values while preserving data consistency.
- Outlier Detection for Anomaly Identification:
- Statistical Methods: Techniques such as z-scores detect anomalies by identifying extreme deviations, helping spot potential equipment failures.
- Machine Learning Algorithms: Models like Isolation Forests and Local Outlier Factor (LOF) efficiently identify irregular patterns, enhancing failure prediction accuracy.
- Normalization:
- Z-score Normalization: Techniques like z-score normalization ensure that the data is on a comparable scale, enhancing model performance.
2.3. Feature Engineering
Feature engineering plays a crucial role in enhancing the accuracy of machine learning models used in predictive maintenance (cPdM). By transforming raw data into meaningful features, it improves the model's ability to identify failure patterns and make accurate predictions.
- Time-Based Features:
- Lag Analysis: Creates lagged variables to capture temporal dependencies, helping the model detect recurring trends and delays in equipment behavior.
- Decomposition: Breaks down time series data into trend, seasonality, and residual components, enhancing the model’s ability to recognize patterns over time.
- Frequency-Based Features:
- Autocorrelation Analysis: Measures the correlation between time series observations at different lags, helping detect repeating cycles and seasonal behaviors.
- Spectral Analysis: Uses techniques like Fast Fourier Transform (FFT) to identify dominant frequencies and uncover periodic patterns that may indicate potential failures.
- Dimensionality Reduction for Noise Elimination:
- Principal Component Analysis (PCA): Reduces the dataset’s complexity by focusing on the most significant features, filtering out irrelevant noise, and enhancing model performance.
2.4. Machine Learning Modeling
Selecting the right machine learning (ML) models is vital for accurate failure prediction and reliable maintenance strategies in cPdM. By leveraging both time series forecasting and classification models, organizations can effectively predict and prevent equipment failures.
- Time Series Forecasting Models:
- ARIMA (Auto Regressive Integrated Moving Average): Ideal for capturing trends and seasonality in time series data, making it suitable for predicting maintenance schedules and failure occurrences.
- LSTM (Long Short-Term Memory) Networks: A type of recurrent neural network (RNN) designed for sequential data, making it effective in learning long-term dependencies and detecting complex patterns in equipment behavior.
- Classification Models:
- Support Vector Machines (SVM): Effective for binary classification tasks, such as differentiating between healthy and faulty equipment, enabling proactive maintenance decisions.
- Random Forests & Decision Trees: These models categorize equipment conditions by identifying failure patterns and detecting root causes of malfunctions.
2.5. Dashboarding and Reporting
Visualization tools play a crucial role in making predictive maintenance insights easily accessible to stakeholders. These dashboards enable data-driven decision-making by presenting key metrics in a clear and actionable format.
- Engineering Dashboard:
- Displays insights into failure modes, downtime costs, and key operational parameters, helping teams identify and address potential issues efficiently.
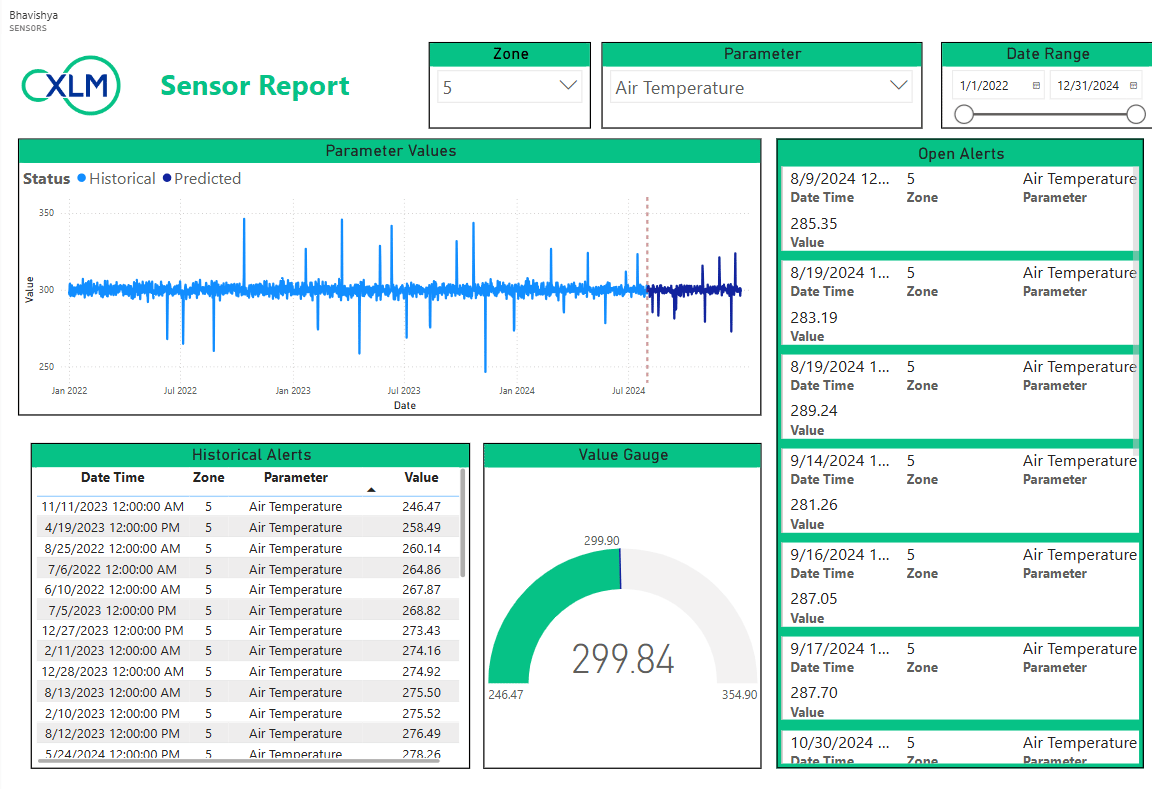
- Operations Dashboard:
- Displays predicted failure trends and provides detailed failure insights, enabling proactive maintenance actions to prevent unexpected downtime and optimize resource allocation.
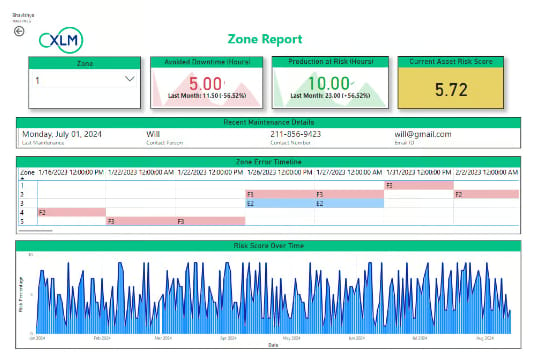
- Facilities Management Benefits:
- Optimizes spare parts management by accurately predicting maintenance needs, reducing unnecessary inventory costs.
- Integrates maintenance history to enhance planning and scheduling efficiency, ensuring timely and effective maintenance interventions.

2.6. Key Performance Indicators (KPIs)
To effectively manage Continuous Predictive Maintenance (cPdM), organizations must establish Key Performance Indicators (KPIs). These metrics enable data-driven decision-making by tracking maintenance efficiency, predicting equipment failures, and optimizing operational performance.
- Mean Time Between Failure (MTBF):
- Measures the average time interval between equipment failures, indicating reliability.
- A higher MTBF reflects fewer breakdowns, showcasing improved system stability.
- Mean Time to Repair (MTTR):
- Assesses repair efficiency by calculating the average time required to fix failed equipment.
- A lower MTTR indicates faster repair processes, minimizing downtime costs.
- Expected Next Failure Date:
- Utilizes historical failure data and predictive models to estimate when the next failure is likely to occur.
- Helps in proactive maintenance scheduling, reducing unplanned downtime and optimizing resource planning.
3.0. Key Enhancements Through Integration
Integrating Industrial DataOps with Continuous Predictive Maintenance (cPdM) significantly enhances maintenance efficiency and effectiveness in industrial environments. This powerful combination creates a comprehensive framework that boosts operational performance, reduces maintenance costs, and increases overall equipment reliability.
By merging Industrial DataOps with cPdM, organizations can improve data quality and accessibility, ensuring that predictive models are built on accurate, real-time data. This leads to more precise failure forecasts and proactive maintenance actions. Additionally, this integration promotes cost efficiency by optimizing resource allocation and reducing unplanned downtime.
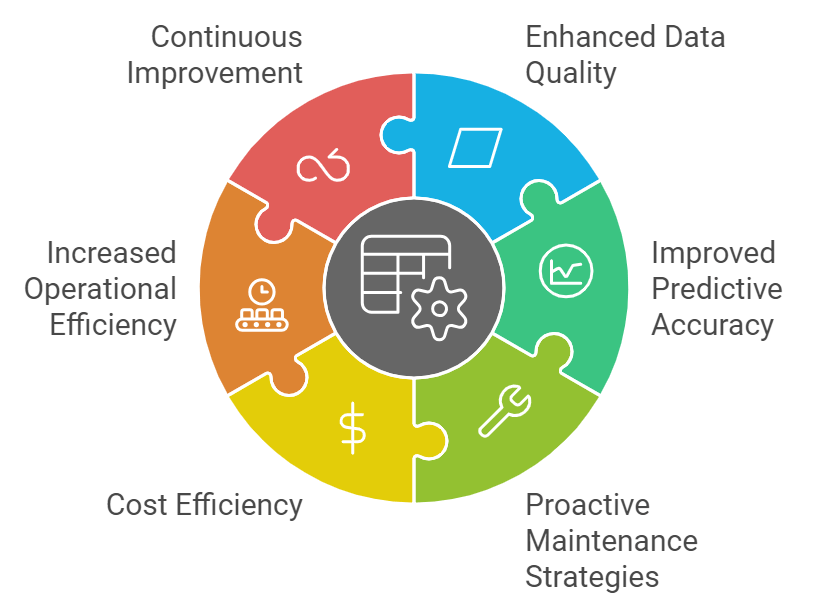
Furthermore, it fosters continuous improvement by enabling real-time insights, iterative model refinement, and adaptive strategies. This holistic approach drives substantial productivity gains while mitigating risks associated with unexpected equipment failures, positioning organizations for long-term operational success.
3.1. Enhanced Data Quality and Accessibility
- Streamlined Data Management:
- Industrial DataOps seamlessly integrates data from multiple sources, including sensors, CMMS, and operational systems.
- This ensures predictive models are built on high-quality, relevant data, leading to more accurate failure predictions.
- Real-Time Data Processing:
- The ability to process data in real-time enables continuous equipment monitoring.
- Organizations can detect anomalies early and predict failures as they emerge.
- This immediacy supports faster, data-driven maintenance decisions.
3.2. Improved Predictive Accuracy
- Advanced Analytics Techniques:
- By leveraging machine learning algorithms and statistical models, Industrial DataOps improves the accuracy of predictive maintenance.
- Techniques like time series analysis, regression models, and classification algorithms identify failure patterns and forecast potential breakdowns.
- Enhanced Feature Engineering:
- DataOps facilitates robust feature engineering, transforming raw sensor data into meaningful insights.
- Techniques such as lag analysis and frequency-based analysis capture trends and seasonality, boosting model performance.
3.3. Proactive Maintenance Strategies
- Shift from Reactive to Proactive Maintenance:
- The integration allows organizations to anticipate failures and schedule maintenance during planned downtimes, reducing disruptions.
- This proactive approach enhances equipment reliability and production continuity.
- Reduction of Over-Maintenance:
- Accurate failure predictions prevent unnecessary maintenance activities, reducing wasted labor and resource costs.
- This also extends equipment lifespan and optimizes operational performance.
3.4. Cost Efficiency
- Optimized Resource Allocation:
- With precise failure predictions, organizations can allocate workforce and spare parts more effectively.
- This prevents overstocking while ensuring essential components are readily available.
- Reduced Downtime Costs:
- Minimizing unplanned downtime significantly reduces the financial impact of lost production and emergency repairs.
- This translates into higher cost efficiency and improved profitability.
3.5. Increased Operational Efficiency
- Downtime Reduction:
- Accurate failure predictions enable timely interventions, minimizing downtime and maximizing asset availability.
- This enhances overall productivity and reduces production losses.
- Enhanced Decision-Making Through Visualization:
- Interactive dashboards integrated into DataOps provide stakeholders with access to actionable insights through visualizations displaying key performance indicators (KPIs) such as Mean Time Between Failures (MTBF) and Mean Time to Repair (MTTR).
- These visualizations help teams quickly identify trends and make informed decisions regarding maintenance strategies.
3.6. Continuous Improvement
- Feedback Mechanisms:
- The integration of DataOps and cPdM creates feedback loops where insights from predictive maintenance drive continuous optimization.
- This iterative process refines machine learning models and enhances predictive accuracy over time.
- Adaptability to Change:
- Organizations can swiftly adapt maintenance strategies based on new data or operational shifts.
- This ensures ongoing process optimization and responsiveness to changing conditions.
4.0. Conclusion
The integration of Industrial DataOps with Continuous Predictive Maintenance (cPdM) marks a transformative shift in how organizations approach maintenance strategies. By adopting data-driven methodologies, companies can significantly enhance their predictive capabilities, resulting in reduced downtime, optimized resource allocation, and improved operational efficiency.
The systematic application of Industrial DataOps enables seamless data collection, integration, and processing from multiple sources, including sensors, CMMS, and operational systems. This ensures real-time monitoring and analysis, allowing organizations to detect anomalies early and predict potential failures with greater accuracy. This proactive approach minimizes the risks associated with unexpected equipment breakdowns while driving cost savings through optimized resource management.
Moreover, the use of advanced analytics and machine learning techniques continuously refines predictive models. Through data preprocessing and feature engineering, organizations can ensure their models leverage high-quality, reliable data, boosting the accuracy of failure predictions. Interactive dashboards and visualization tools further enhance decision-making processes by providing actionable insights into maintenance trends, equipment conditions, and potential risks.
In essence, the synergistic integration of Industrial DataOps and cPdM empowers organizations to transition from reactive to proactive maintenance, driving continuous improvement. This shift is critical for sustaining equipment reliability and operational excellence in today’s competitive industrial landscape. Companies that embrace this data-driven transformation will benefit from increased productivity, reduced operational costs, and extended equipment lifespans, positioning themselves for long-term success in an increasingly data-centric world.
5.0. Related Posts
- Industrial DataOps: Real-Time Insights for Industry 4.0
- How Industrial DataOps Improves Data Security & Compliance
6.0. ContinuousTV Audio Podcasts
- AP007: Is your PLC an MTP based on Margo?
- AP008: Industrial DataOps - Part 1
- AP009: Industrial DataOps - Part 2
7.0. Latest AI News
- 𝗜𝗺𝗮𝗴𝗶𝗻𝗲 𝗮 𝘄𝗼𝗿𝗹𝗱 𝘄𝗵𝗲𝗿𝗲 𝗔𝗜 𝘀𝗲𝗲𝘀 𝗮𝗻𝗱 𝘂𝗻𝗱𝗲𝗿𝘀𝘁𝗮𝗻𝗱𝘀 𝗹𝗶𝗸𝗲 𝗵𝘂𝗺𝗮𝗻𝘀—𝘄𝗲𝗹𝗰𝗼𝗺𝗲 𝘁𝗼 𝘁𝗵𝗲 𝗳𝘂𝘁𝘂𝗿𝗲 𝗼𝗳 𝘀𝗲𝗮𝗿𝗰𝗵 𝘄𝗶𝘁𝗵 𝗖𝗼𝗵𝗲𝗿𝗲'𝘀 𝗠𝘂𝗹𝘁𝗶𝗺𝗼𝗱𝗮𝗹 𝗘𝗺𝗯𝗲𝗱 𝟯.
- 𝗖𝗮𝗻 𝗔𝗜 𝗿𝗲𝗽𝗹𝗮𝗰𝗲 𝗵𝘂𝗺𝗮𝗻 𝘁𝗲𝗮𝗰𝗵𝗲𝗿𝘀? 𝗧𝗵𝗶𝘀 𝗧𝗲𝘅𝗮𝘀 𝘀𝗰𝗵𝗼𝗼𝗹 𝗺𝗶𝗴𝗵𝘁 𝗵𝗮𝘃𝗲 𝘁𝗵𝗲 𝗮𝗻𝘀𝘄𝗲𝗿
- 𝗜𝗺𝗮𝗴𝗶𝗻𝗲 𝗱𝗶𝗮𝗴𝗻𝗼𝘀𝗶𝗻𝗴 𝗰𝗼𝗺𝗽𝗹𝗲𝘅 𝗱𝗶𝘀𝗲𝗮𝘀𝗲𝘀 𝗶𝗻 𝘁𝗵𝗲 𝘁𝗶𝗺𝗲 𝗶𝘁 𝘁𝗮𝗸𝗲𝘀 𝘁𝗼 𝗯𝗿𝗲𝘄 𝗮 𝗰𝘂𝗽 𝗼𝗳 𝗰𝗼𝗳𝗳𝗲𝗲.
- Amazon has made a strategic agreement with Covariant, an AI robotics startup, that could potentially revolutionize its warehouse operations.
8.0. FAQs
share this